In the field of permanent magnetic materials, NdFeB magnets have become the core materials of high-end fields such as new energy vehicles, precision medical equipment, and industrial robots due to their excellent magnetic properties and energy density. However, in actual engineering applications, more than 60% of magnet failure cases are not caused by defects in the material itself, but by misjudgment of size and shape during the selection stage. This data reveals a key fact: the selection of magnet parameters is essentially a precise game between multi-dimensional physical quantities.
1. Size parameters: a balance between magnetic properties and physical limits
The magnetic energy product (BHmax) of NdFeB magnets shows nonlinear characteristics with size changes. When the magnet thickness (magnetization direction size) is less than the critical value (usually 3-5mm), the demagnetization field effect will cause the remanence Br to drop significantly. For example, when the thickness of a certain N52 brand magnet is reduced from 5mm to 1mm, its effective magnetic energy product will decay by nearly 40%. This size effect is particularly critical in micro-motor design, and engineers must accurately calculate the effective magnetic field distribution in the magnetic circuit through finite element simulation.
In terms of combating physical limits, the processing of thin magnets (<2mm) requires breaking through the limitations of traditional cutting processes. The combination of wire cutting and ion beam surface treatment technology can control the thickness tolerance within ±0.02mm, which is crucial for the application of magnetic encoders in precision sensors. At the same time, the aspect ratio (L/D) of the magnet directly affects the utilization rate of the coercive force Hcj. When L/D<0.5, the risk of irreversible loss under the action of the reverse magnetic field will increase sharply.
2. Shape design: the art of flux manipulation
The topological optimization of magnet shape is triggering a revolution in magnetic circuit design. The open magnetic circuit generated by traditional block magnets often causes more than 30% of magnetic energy waste, while directional energy flow control can be achieved through shape innovation. For example:
The fan-shaped cross-section magnetic ring (120° arc segment) can improve the air gap magnetic flux uniformity by 15% in the servo motor
The tapered end face design reduces the contact force fluctuation of the magnetic latching relay to within ±2%
The multi-pole magnetized tile-shaped magnet builds an ultra-uniform static magnetic field of 0.5ppm in the MRI device
The conflict between shape parameters and assembly constraints requires creative solutions. A drone gimbal stabilization system uses a nested trapezoidal magnet group, which compresses the axial space by 42% while keeping the total magnetic energy product unchanged. This involves complex magnetic moment vector synthesis calculations, which require iterative optimization with the help of the Maxwell stress tensor model.
3. Selection decision tree: Pareto optimality of cost and performance
To establish a scientific selection decision model, it is necessary to construct a multi-dimensional parameter space: variables such as magnetic energy product requirements, temperature coefficients, corrosion resistance levels, space constraints, and dynamic load spectra constitute hypersurface equations. Experience shows that the three-stage screening strategy can improve the selection efficiency:
Physical feasibility screening: Eliminate candidate solutions that cannot meet the basic field strength requirements through the Stoner-Wohlfarth model
Process cost evaluation: The processing cost of special-shaped magnets usually increases exponentially, and it is necessary to establish a quantitative relationship between the shape complexity factor (SCF) and the processing time
Full life cycle verification: including temperature cycle test (-50℃~200℃), impact vibration test (20g, 2000Hz), and 10-year magnetic attenuation simulation
In the case of new energy vehicle drive motors, by replacing traditional rectangular magnets with wavy cross-section designs, the amount of rare earth materials is reduced by 18% while keeping the output torque unchanged, and the eddy current loss is reduced to 63% of the original level. The direct benefit of this optimization is that the motor system efficiency is increased by 1.2 percentage points, which is equivalent to an increase of 5-8 kilometers in the vehicle's cruising range.
Fourth, cutting-edge breakthroughs: Additive manufacturing can reconstruct the shape
Selective laser melting (SLM) technology is breaking through the morphological limitations of traditional powder metallurgy processes. A German laboratory has successfully prepared NdFeB magnets with gradient porosity inside. This bionic structure reduces eddy current loss to 1/5 of that of traditional dense magnets while maintaining magnetic properties. A more revolutionary development is 4D printed magnets, whose shape can be controllably deformed with temperature or electric field, which opens up new possibilities for adaptive magnetic circuit systems.
In the era of Industry 4.0, the selection of NdFeB magnets has gone beyond simple parameter matching and evolved into a system-level innovation that integrates electromagnetism, materials science, and topology optimization. Mastering the deep mechanism of size and shape means obtaining the key to open the door to efficient electromagnetic energy - this is not only the art of technology selection, but also a strategic layout for future competitiveness.
HC Magnets
The company has eight advanced production lines of electroplating process, which can fully ensure customers' various difficult requirements for product coating. And relying on Ningbo's strong front processing capacity, it can stably process and produce N52,N42,N50M,N48H, and other high-performance ndFeb. We are well-known in China and have received welcome from various buyers for on-site inspections, Accept testing and provide free samples Founded in 2017, formerly known as Hangzhou Jiahe Magnetic Ware Factory was established in 2005, Hangzhou Heci Technology Co., Ltd. has been engaged in magnetic industry for 18 years. It is a new high-tech enterprise integrating production, processing, and sales, specializing in the production of permanent magnet materials such as NdFeB magnets. The company is now located in Ningbo, the eastern port city of Yangtze River Delta. The company has the capacity of processing 1000 tons of high performance NdFeB magnets per year. Our products are mainly sold to India, Vietnam and Germany.
Resources
News
- What are the advantages of using NdFeB Magnets in medical devices?
- Size and shape selection of NdFeB magnets: a key game in engineering applications
- What is the important role of NdFeB Magnets in automobile manufacturing?
- How to determine the magnetic field strength requirements of NdFeB Magnets in specific applications?
- Why NdFeB Magnets are the preferred magnetic material in modern motors and generators?
- How do NdFeB Magnets improve the power output of power tools?
- How do NdFeB Magnets help improve the efficiency of wind turbines?
- How to use NdFeB Magnets to improve the battery performance of electric vehicles?
- How to reduce the demagnetization of NdFeB Magnets?
- When using NdFeB Magnets, how to prevent them from interfering with other devices?
- How to Choose NdFeB Magnets for High-Density Applications?
- How to use NdFeB magnets to improve the accuracy of precision instruments?
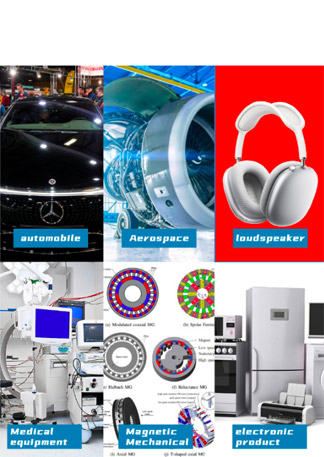