As the third-generation rare earth permanent magnet material, NdFeB Magnets are widely used in high-tech fields such as medical equipment, new energy vehicles, and industrial motors due to their excellent magnetic properties and stable physical properties. In specific application scenarios, determining the appropriate magnetic field strength is a key link to ensure equipment performance and reliability.
1. Deconstruction of engineering requirements for application scenarios
The first step to clarify the magnetic field strength is to deeply analyze the core demands of the target application. Taking the magnetic resonance imaging (MRI) system as an example, its working magnetic field must simultaneously meet high uniformity (deviation does not exceed 50ppm) and a specific field strength range (0.35T-7T); while the electric vehicle drive motor requires the magnetic field to have high stability (temperature rise fluctuation <5%) and dynamic response characteristics. Engineers need to establish a demand parameter matrix, including 12 key indicators such as operating temperature range, space constraints, and dynamic load characteristics, and determine the weight coefficient of each parameter through the analytic hierarchy process (AHP).
2. Magnetic circuit design and simulation verification
The magnetic circuit model established based on the Maxwell equations is the theoretical basis for determining the magnetic field strength. When using finite element analysis software (such as ANSYS Maxwell) for three-dimensional magnetic field simulation, it is necessary to focus on the geometry of the magnetic conductor, the arrangement of the magnetic poles, and the magnetic interference effect of adjacent components. Experimental data show that the surface field strength can be increased by 0.12T for every 1mm increase in magnet thickness, but the magnetic circuit structure needs to be optimized simultaneously to prevent the magnetic leakage rate from exceeding the critical value of 15%. Typical cases show that the air gap flux density of permanent magnet motors can be increased by 18.7% through topology optimization.
3. Material properties and environmental adaptation
Different brands of NdFeB magnets (such as N52, 35SH) have significant differences in key parameters such as remanence (Br) and coercivity (Hcj). When the application ambient temperature exceeds 80℃, high coercivity materials with Hcj values greater than 20kOe should be selected to compensate for the magnetic loss caused by the reversible temperature coefficient (-0.12%/℃). In a corrosive environment, the surface magnetic field attenuation rate of magnets with nickel-copper-nickel triple electroplating can be controlled within 0.5% per year.
IV. Experimental verification and iterative optimization
Establishing a prototype test system is a necessary step in verifying the magnetic field strength. When using a Gaussmeter for measurement, the measurement specifications specified in the ISO 21782 standard should be followed to ensure that the probe positioning error is less than 0.1mm. The magnetic field stability test under dynamic conditions needs to last for more than 200 hours, and the long-term working reliability is evaluated by the magnetic flux attenuation curve (Δt-Φ). A case of an industrial robot joint motor shows that after three design iterations, its working point magnetic field strength is optimized from the initial design of 0.85T to 0.92T, and the efficiency is improved by 9.3%.
V. Systematic design process construction
It is recommended to use the PDCA (Plan-Do-Check-Act) cycle to establish a systematic design process: in the early stage, QFD (Quality Function Deployment) is used to convert user needs into technical indicators; in the mid-term, TRIZ theory is used to solve the contradictions in magnetic circuit design; in the later stage, the Taguchi method is used to optimize parameters. In the application practice of wind turbines, this process successfully reduced the magnetic field strength deviation from ±7% to ±2.5%.
HC Magnets
The company has eight advanced production lines of electroplating process, which can fully ensure customers' various difficult requirements for product coating. And relying on Ningbo's strong front processing capacity, it can stably process and produce N52,N42,N50M,N48H, and other high-performance ndFeb. We are well-known in China and have received welcome from various buyers for on-site inspections, Accept testing and provide free samples Founded in 2017, formerly known as Hangzhou Jiahe Magnetic Ware Factory was established in 2005, Hangzhou Heci Technology Co., Ltd. has been engaged in magnetic industry for 18 years. It is a new high-tech enterprise integrating production, processing, and sales, specializing in the production of permanent magnet materials such as NdFeB magnets. The company is now located in Ningbo, the eastern port city of Yangtze River Delta. The company has the capacity of processing 1000 tons of high performance NdFeB magnets per year. Our products are mainly sold to India, Vietnam and Germany.
Resources
News
- Can NdFeB Magnets Retain Their Strength in High-Temperature Environments?
- How to ensure the performance stability of NdFeB magnets in daily use?
- What Are the Key Factors to Consider When Choosing NdFeB Magnets for Motors?
- How Do NdFeB Magnets Compare to Other Permanent Magnets in Industrial Applications?
- What are the advantages of using NdFeB Magnets in medical devices?
- Size and shape selection of NdFeB magnets: a key game in engineering applications
- What is the important role of NdFeB Magnets in automobile manufacturing?
- How to determine the magnetic field strength requirements of NdFeB Magnets in specific applications?
- Why NdFeB Magnets are the preferred magnetic material in modern motors and generators?
- How do NdFeB Magnets improve the power output of power tools?
- How do NdFeB Magnets help improve the efficiency of wind turbines?
- How to use NdFeB Magnets to improve the battery performance of electric vehicles?
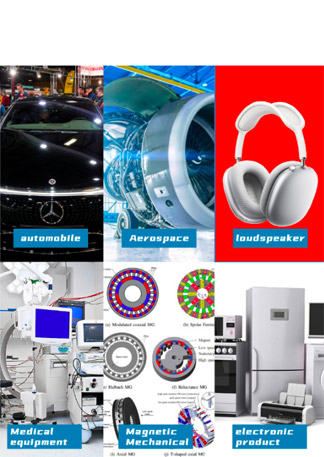