In the trend of modern industry towards high efficiency, lightweight and energy saving, neodymium iron boron (NdFeB) permanent magnet materials have gradually become the core materials for motor and generator design due to their excellent performance. From electric vehicle drive systems to wind turbines, from consumer electronics to aerospace, the application of NdFeB magnets is reshaping the boundaries of energy conversion technology.
1. Subversive breakthrough in magnetic properties
The biggest advantage of neodymium iron boron magnets is their extremely high magnetic energy product (BHmax). The magnetic energy product of the third-generation sintered NdFeB can reach 50-55 MGOe (mega gauss oersted), far exceeding ferrite magnets (3-5 MGOe) and samarium cobalt magnets (25-32 MGOe). This means that at the same output power, the size of the motor using NdFeB can be reduced by 30%-50% and the weight can be reduced by more than 40%. Taking the drive motor of Tesla Model 3 as an example, it adopts a six-pole NdFeB magnet design, with a power density of 6 kW/kg and an efficiency of over 97%, which is directly attributed to the leap in magnet performance.
2. Engineering breakthrough in high-temperature stability
The fatal weakness of early NdFeB magnets was **low Curie temperature (about 310℃)** and high-temperature demagnetization problems. By adding heavy rare earth elements such as dysprosium (Dy) and terbium (Tb), combined with grain boundary diffusion technology, modern N series (temperature resistance 120℃) and EH series (temperature resistance 200℃) magnets can work stably in harsh environments. The gradient magnet design adopted by Toyota Prius hybrid system customizes the rare earth ratio in different areas of the rotor, so that the motor still maintains a magnetic flux attenuation of less than 5% under -40℃ to 180℃ working conditions.
3. Paradigm shift in economic benefits
Although the raw material cost of NdFeB magnets is higher than that of traditional magnets, its full life cycle cost advantage is significant. After wind turbines adopted NdFeB, the rare earth consumption per unit of power generation decreased by 60% compared with ten years ago. Siemens Gamesa's direct-drive permanent magnet wind turbine reduces annual operation and maintenance costs by 25% due to the elimination of gearboxes and reduced copper consumption. More noteworthy is that the maturity of magnet recovery technology (such as hydrogen crushing) has enabled the rare earth recycling rate to reach more than 95%, forming a closed loop of resources.
4. Deep penetration of multi-dimensional application scenarios
In the field of electric vehicles, the fifth-generation eDrive system of BMW iX optimizes the magnetic field distribution through the Halbach magnet array, achieving a 30% increase in torque density. In the field of precision control, the joint motor of the collaborative robot uses bonded NdFeB, which still maintains zero heat generation characteristics at a positioning accuracy of 0.1 mm. Even in extreme scenarios, the electric turbine pump of the SpaceX starship relies on nickel-plated NdFeB magnets to resist ultra-low temperature corrosion in liquid oxygen environments.
5. Future-oriented technological evolution
Facing the geopolitical risks of rare earth resources, the industry is making breakthroughs along two paths: on the one hand, through grain refinement (grain size <3μm) and magnetic texture control technology, high-performance magnets with low heavy rare earth (<2%) are developed; on the other hand, Toyota and other companies have developed a prototype of rare earth-free iron-nickel (LNP-FeNi) magnets. Although the magnetic energy product is only 1.4 T, it points the way to complete de-rare earthization.
NdFeB magnets are triggering a silent energy revolution. It is not only a victory of materials science, but also a concentrated embodiment of system engineering thinking - through the precise control of microscopic lattice structure, the leapfrog improvement of macroscopic equipment performance is achieved. With the integration of 3D printing magnet technology and artificial intelligence material design, the energy efficiency boundary of future motor systems may be redefined again. In this process, the technological iteration of NdFeB materials will continue to lead industry changes.
HC Magnets
The company has eight advanced production lines of electroplating process, which can fully ensure customers' various difficult requirements for product coating. And relying on Ningbo's strong front processing capacity, it can stably process and produce N52,N42,N50M,N48H, and other high-performance ndFeb. We are well-known in China and have received welcome from various buyers for on-site inspections, Accept testing and provide free samples Founded in 2017, formerly known as Hangzhou Jiahe Magnetic Ware Factory was established in 2005, Hangzhou Heci Technology Co., Ltd. has been engaged in magnetic industry for 18 years. It is a new high-tech enterprise integrating production, processing, and sales, specializing in the production of permanent magnet materials such as NdFeB magnets. The company is now located in Ningbo, the eastern port city of Yangtze River Delta. The company has the capacity of processing 1000 tons of high performance NdFeB magnets per year. Our products are mainly sold to India, Vietnam and Germany.
Resources
News
- Can NdFeB Magnets Retain Their Strength in High-Temperature Environments?
- How to ensure the performance stability of NdFeB magnets in daily use?
- What Are the Key Factors to Consider When Choosing NdFeB Magnets for Motors?
- How Do NdFeB Magnets Compare to Other Permanent Magnets in Industrial Applications?
- What are the advantages of using NdFeB Magnets in medical devices?
- Size and shape selection of NdFeB magnets: a key game in engineering applications
- What is the important role of NdFeB Magnets in automobile manufacturing?
- How to determine the magnetic field strength requirements of NdFeB Magnets in specific applications?
- Why NdFeB Magnets are the preferred magnetic material in modern motors and generators?
- How do NdFeB Magnets improve the power output of power tools?
- How do NdFeB Magnets help improve the efficiency of wind turbines?
- How to use NdFeB Magnets to improve the battery performance of electric vehicles?
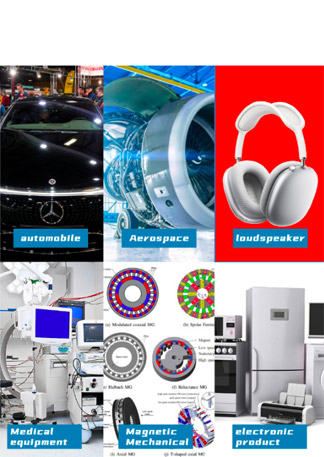