Since its advent in the 1980s, neodymium iron boron (NdFeB) permanent magnets have become the "magnetic king" of modern industry with their excellent magnetic properties. Its magnetic energy product (BHmax) is as high as 50 MGOe or more, far exceeding traditional magnetic materials such as ferrite and aluminum nickel cobalt, and has become one of the core materials for the transformation of the automotive industry to electrification and intelligence. In the field of automobile manufacturing, the application of NdFeB magnets not only improves vehicle performance, but also promotes the realization of energy conservation and emission reduction goals.
1. Driving the electrification revolution: the core of the motor system
In the field of new energy vehicles, NdFeB magnets are the core materials of permanent magnet synchronous motors (PMSM). This type of motor relies on the high remanence (Br) and coercive force (Hcj) of neodymium iron boron, which can maintain stable output at high temperature and high speed. Taking Tesla Model 3 as an example, its drive motor uses sintered neodymium iron boron magnets, which has a power density increased by 30% compared with traditional motors and a cruising range increased by more than 15%. In addition, the auxiliary motor and start-stop system of hybrid vehicles also rely on NdFeB magnets to achieve fast response and high-efficiency conversion.
Technical advantages:
The volume is reduced by 50%, the weight is reduced by 40%, which helps to reduce the weight of the car;
The power conversion efficiency exceeds 95%, reducing energy waste;
High temperature stability (operating temperature can reach 200℃) adapts to harsh working conditions.
2. Empowering intelligence: the "invisible pusher" of sensors and actuators
The intelligent driving system equipped in modern cars relies on a large number of precision sensors, and NdFeB magnets are the key components of these devices. For example:
Electronic power steering system (EPS): The micro magnets in the Hall sensor monitor the steering wheel torque in real time to improve the control accuracy;
Anti-lock braking system (ABS): The magnetic encoder is used to detect the wheel speed to ensure the safety of emergency braking;
In-vehicle radar and camera: The magnet is used for motor-driven lens focus and radar beam control to enhance the reliability of autonomous driving.
These applications place extremely high demands on the dimensional accuracy and stability of magnets, and NdFeB can meet the micron-level tolerance requirements through sintering, plating and other processes.
3. Dual Value of Energy Saving and Environmental Protection
The International Energy Agency (IEA) study shows that electric vehicles using NdFeB permanent magnet motors have carbon emissions per kilometer lower than fuel vehicles by more than 60%. At the same time, the advancement of magnet recycling technology (such as hydrogen crushing method) has made the recycling rate of rare earth elements such as neodymium and dysprosium exceed 90%, alleviating the problem of resource dependence. BMW, Toyota and other automakers have established a closed-loop recycling system to re-purify magnets in retired motors.
4. Challenges and Future Trends
Although NdFeB magnets have significant advantages, their costs are greatly affected by fluctuations in rare earth prices. To this end, the industry is breaking through bottlenecks through technological innovation:
Grain boundary diffusion technology: reduce the amount of heavy rare earths and reduce material costs by 20%;
Bonded NdFeB: customize complex-shaped magnets through 3D printing to expand application scenarios;
Heavy rare earth-free formula: develop alternatives to praseodymium and cerium to improve supply chain security.
HC Magnets
The company has eight advanced production lines of electroplating process, which can fully ensure customers' various difficult requirements for product coating. And relying on Ningbo's strong front processing capacity, it can stably process and produce N52,N42,N50M,N48H, and other high-performance ndFeb. We are well-known in China and have received welcome from various buyers for on-site inspections, Accept testing and provide free samples Founded in 2017, formerly known as Hangzhou Jiahe Magnetic Ware Factory was established in 2005, Hangzhou Heci Technology Co., Ltd. has been engaged in magnetic industry for 18 years. It is a new high-tech enterprise integrating production, processing, and sales, specializing in the production of permanent magnet materials such as NdFeB magnets. The company is now located in Ningbo, the eastern port city of Yangtze River Delta. The company has the capacity of processing 1000 tons of high performance NdFeB magnets per year. Our products are mainly sold to India, Vietnam and Germany.
Resources
News
- What are the advantages of using NdFeB Magnets in medical devices?
- Size and shape selection of NdFeB magnets: a key game in engineering applications
- What is the important role of NdFeB Magnets in automobile manufacturing?
- How to determine the magnetic field strength requirements of NdFeB Magnets in specific applications?
- Why NdFeB Magnets are the preferred magnetic material in modern motors and generators?
- How do NdFeB Magnets improve the power output of power tools?
- How do NdFeB Magnets help improve the efficiency of wind turbines?
- How to use NdFeB Magnets to improve the battery performance of electric vehicles?
- How to reduce the demagnetization of NdFeB Magnets?
- When using NdFeB Magnets, how to prevent them from interfering with other devices?
- How to Choose NdFeB Magnets for High-Density Applications?
- How to use NdFeB magnets to improve the accuracy of precision instruments?
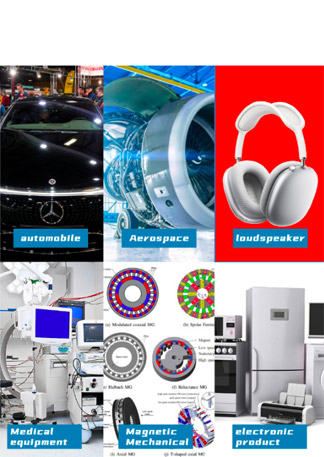