In the realm of industrial applications, permanent magnets are indispensable components, driving innovations in sectors ranging from renewable energy to robotics. Among these materials, neodymium-iron-boron (NdFeB) magnets have emerged as a dominant force, but how do they stack up against traditional alternatives like ferrite, alnico, and samarium-cobalt (SmCo) magnets?
1. Magnetic Strength: The Unmatched Power of NdFeB
NdFeB magnets reign supreme in terms of energy density, quantified by their maximum energy product (BHmax). With BHmax values exceeding 50 MGOe (Mega-Gauss Oersteds), NdFeB magnets deliver 5–10 times the magnetic strength of ferrite magnets and twice that of SmCo magnets. This exceptional performance makes them ideal for applications requiring compact size and high power, such as electric vehicle motors, wind turbine generators, and precision medical devices.
In contrast, ferrite magnets (BHmax: 3–5 MGOe) and alnico magnets (BHmax: 5–10 MGOe) struggle to compete in high-efficiency scenarios. While SmCo magnets (BHmax: 25–32 MGOe) offer respectable strength, their higher cost and limited availability often relegate them to niche applications like aerospace or defense systems.
2. Temperature Stability: Balancing Performance and Limitations
One critical limitation of standard NdFeB magnets is their sensitivity to high temperatures. Standard grades (N-Series) lose magnetic strength above 80°C, though advanced grades (EH, AH) with dysprosium or terbium additives can operate up to 220°C. This makes them suitable for most industrial environments but still less robust than SmCo magnets, which retain stability up to 350°C.
Alnico magnets, withstanding temperatures up to 540°C, excel in extreme-heat applications like sensors in combustion engines. Ferrite magnets, while thermally stable up to 250°C, suffer from low intrinsic coercivity, making them prone to demagnetization under mechanical stress.
Key Takeaway: For industries requiring both high strength and moderate heat resistance (e.g., industrial automation, HVAC systems), NdFeB remains the optimal choice. SmCo or alnico are reserved for extreme thermal or corrosive environments.
3. Corrosion Resistance and Durability
NdFeB magnets are prone to oxidation due to their iron-rich composition. To mitigate this, industrial-grade NdFeB magnets are typically coated with nickel, zinc, or epoxy. Even with coatings, they may underperform in highly corrosive environments compared to SmCo or ferrite magnets, which exhibit innate corrosion resistance.
However, advancements in protective coatings and alloy modifications (e.g., adding cobalt) have significantly improved NdFeB’s durability. For example, marine energy systems and automotive applications now widely adopt coated NdFeB magnets without compromising longevity.
4. Cost-Effectiveness: A Driving Factor for Industrial Adoption
Despite their superior performance, NdFeB magnets are more expensive than ferrite or alnico. However, their high energy density reduces the required magnet volume in designs, lowering overall system costs. For instance, a smaller NdFeB magnet can replace a bulkier ferrite magnet in a motor, saving space and material while boosting efficiency.
SmCo magnets, while offering excellent temperature stability, are 2–3 times more expensive than NdFeB due to scarce rare-earth elements (samarium and cobalt). This limits their use to mission-critical applications where cost is secondary to reliability.
5. Sustainability and Supply Chain Considerations
NdFeB magnets rely on neodymium and other rare-earth elements, raising concerns about supply chain stability. However, recycling programs and efforts to diversify mining sources (e.g., projects in Australia and the U.S.) are mitigating these risks. Ferrite magnets, made from abundant iron oxide and strontium/carbonates, face fewer supply constraints but cannot match NdFeB’s performance.
HC Magnets
The company has eight advanced production lines of electroplating process, which can fully ensure customers' various difficult requirements for product coating. And relying on Ningbo's strong front processing capacity, it can stably process and produce N52,N42,N50M,N48H, and other high-performance ndFeb. We are well-known in China and have received welcome from various buyers for on-site inspections, Accept testing and provide free samples Founded in 2017, formerly known as Hangzhou Jiahe Magnetic Ware Factory was established in 2005, Hangzhou Heci Technology Co., Ltd. has been engaged in magnetic industry for 18 years. It is a new high-tech enterprise integrating production, processing, and sales, specializing in the production of permanent magnet materials such as NdFeB magnets. The company is now located in Ningbo, the eastern port city of Yangtze River Delta. The company has the capacity of processing 1000 tons of high performance NdFeB magnets per year. Our products are mainly sold to India, Vietnam and Germany.
Resources
News
- How Do NdFeB Magnets Compare to Other Permanent Magnets in Industrial Applications?
- What are the advantages of using NdFeB Magnets in medical devices?
- Size and shape selection of NdFeB magnets: a key game in engineering applications
- What is the important role of NdFeB Magnets in automobile manufacturing?
- How to determine the magnetic field strength requirements of NdFeB Magnets in specific applications?
- Why NdFeB Magnets are the preferred magnetic material in modern motors and generators?
- How do NdFeB Magnets improve the power output of power tools?
- How do NdFeB Magnets help improve the efficiency of wind turbines?
- How to use NdFeB Magnets to improve the battery performance of electric vehicles?
- How to reduce the demagnetization of NdFeB Magnets?
- When using NdFeB Magnets, how to prevent them from interfering with other devices?
- How to Choose NdFeB Magnets for High-Density Applications?
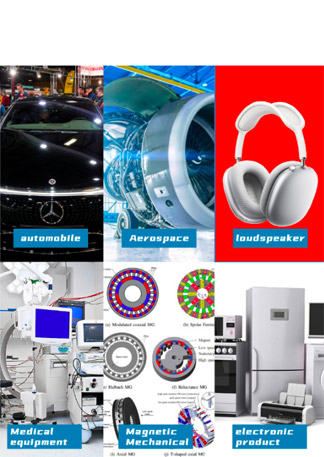