Among the many magnetic materials today, NdFeB Magnets have attracted much attention for their excellent magnetic properties. However, their corrosion resistance and temperature resistance are also key performance indicators that determine their wide application.
The corrosion resistance of NdFeB magnets is an aspect that needs to be considered. Because its main components include metal elements such as neodymium and iron, it is easy to undergo oxidation reactions in some specific environments. In a humid air environment, moisture will react electrochemically with the metal on the surface of the magnet, gradually corroding the magnet, causing its magnetic properties to decrease and possible surface damage. This corrosion phenomenon will be more serious in an environment with corrosive media such as acids and alkalis. For example, in some chemical processing workshops in industrial production, if NdFeB magnets are directly exposed to air containing acidic or alkaline mist, their surfaces will be corroded rapidly, which will not only affect the service life of the magnet itself, but may also cause pollution to surrounding equipment and products.
In order to improve the corrosion resistance of NdFeB magnets, some surface treatment processes are usually used. Common ones include galvanizing, nickel plating, epoxy resin coating, etc. Galvanizing can form a dense zinc layer on the surface of the magnet. Zinc will form a passivation film in the air, which effectively blocks the external moisture and corrosive media from contacting the magnet matrix and plays a protective role. Nickel plating can provide better corrosion resistance and decorativeness. The nickel layer has good chemical stability and can resist the erosion of various acid and alkali solutions. Epoxy resin coating is an organic coating method that can fully cover the surface of the magnet to form an isolation layer to prevent the intrusion of moisture, oxygen and other corrosive substances, while also enhancing the insulation performance of the magnet.
In terms of temperature resistance, NdFeB magnets also have their specific performance. In general, NdFeB magnets can maintain good magnetic properties at room temperature. However, as the temperature rises, its magnetic properties will gradually decrease. When the temperature exceeds a certain range, this downward trend will become more obvious. For example, in some high-temperature industrial environments, such as when a motor is in operation, heat is generated. If the NdFeB magnet is used as a component of the motor, its operating temperature is too high, which will lead to a decrease in the key magnetic parameters such as the remanence and coercive force of the magnet, thereby affecting the efficiency and power output of the motor. However, through some special formulas and process improvements, NdFeB magnets with higher temperature resistance can be developed. For example, by adding certain rare earth elements or using special sintering processes, its Curie temperature can be increased, so that it can still maintain relatively stable magnetic properties at higher temperatures.
In the production process of NdFeB Magnets, our company attaches great importance to the improvement of corrosion resistance and temperature resistance. We have an advanced surface treatment production line, which can accurately provide the most suitable zinc plating, nickel plating or epoxy resin coating treatment for NdFeB magnets according to the different needs of customers, ensuring that they can operate stably and long-term in various corrosive environments. At the same time, our R&D team continues to explore and optimize the formula and manufacturing process of NdFeB magnets, and is committed to developing products with higher temperature resistance to meet the requirements of high-end fields such as aerospace and new energy vehicles for the stable operation of magnetic materials in high temperature environments.
HC Magnets
The company has eight advanced production lines of electroplating process, which can fully ensure customers' various difficult requirements for product coating. And relying on Ningbo's strong front processing capacity, it can stably process and produce N52,N42,N50M,N48H, and other high-performance ndFeb. We are well-known in China and have received welcome from various buyers for on-site inspections, Accept testing and provide free samples Founded in 2017, formerly known as Hangzhou Jiahe Magnetic Ware Factory was established in 2005, Hangzhou Heci Technology Co., Ltd. has been engaged in magnetic industry for 18 years. It is a new high-tech enterprise integrating production, processing, and sales, specializing in the production of permanent magnet materials such as NdFeB magnets. The company is now located in Ningbo, the eastern port city of Yangtze River Delta. The company has the capacity of processing 1000 tons of high performance NdFeB magnets per year. Our products are mainly sold to India, Vietnam and Germany.
Resources
News
- How Do NdFeB Magnets Compare to Other Permanent Magnets in Industrial Applications?
- What are the advantages of using NdFeB Magnets in medical devices?
- Size and shape selection of NdFeB magnets: a key game in engineering applications
- What is the important role of NdFeB Magnets in automobile manufacturing?
- How to determine the magnetic field strength requirements of NdFeB Magnets in specific applications?
- Why NdFeB Magnets are the preferred magnetic material in modern motors and generators?
- How do NdFeB Magnets improve the power output of power tools?
- How do NdFeB Magnets help improve the efficiency of wind turbines?
- How to use NdFeB Magnets to improve the battery performance of electric vehicles?
- How to reduce the demagnetization of NdFeB Magnets?
- When using NdFeB Magnets, how to prevent them from interfering with other devices?
- How to Choose NdFeB Magnets for High-Density Applications?
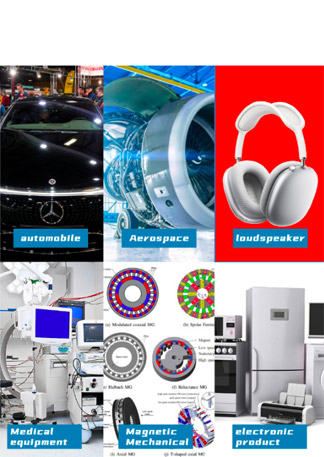