Neodymium iron boron (NdFeB) magnets have been widely used in many fields such as electronics, automobiles, medical equipment, wind power generation, etc. due to their excellent magnetic properties. However, this powerful magnet is prone to corrosion in humid environments, which affects its magnetic properties and service life, becoming one of the bottlenecks restricting its widespread application.
1. Understanding the corrosion mechanism
First of all, it is crucial to understand the corrosion mechanism of NdFeB magnets in humid environments. NdFeB magnets are mainly composed of neodymium, iron, boron and other elements. These elements are prone to chemical reactions with oxygen, moisture and possible chloride ions in the air under humid conditions, resulting in surface oxidation and rust, which in turn affects the magnetic properties and structural integrity of the magnet.
2. Surface treatment technology
Electroplating: By plating a layer of corrosion-resistant metal (such as nickel, zinc, chromium, etc.) on the surface of the magnet, a protective barrier is formed to effectively isolate the magnet from direct contact with the environment and reduce the possibility of corrosion. The electroplating layer not only improves the corrosion resistance of the magnet, but also improves its appearance and wear resistance.
Chemical conversion film: such as phosphate conversion film (phosphating), a dense protective film is formed on the surface of the magnet through chemical reaction. This film can effectively block the intrusion of moisture and corrosive media and improve the corrosion resistance of the magnet.
Organic coating: Magnets are coated with organic materials such as epoxy resin and polyurethane. These coatings not only have good anti-corrosion properties, but also provide certain insulation and mechanical strength to protect the magnets from physical damage and chemical erosion.
3. Environmental control
Reduce humidity: By installing dehumidification equipment and using desiccants, the humidity of the magnet storage and use environment is kept low to reduce the erosion of moisture on the magnet.
Sealed packaging: Place the magnet in a sealed container and fill it with desiccant or inert gas (such as nitrogen) to isolate the external humid air and extend the shelf life of the magnet.
Regular inspection and maintenance: For magnets that are in a humid environment for a long time, regular appearance inspection and performance testing should be carried out to promptly detect and deal with possible corrosion problems to avoid further deterioration of corrosion.
4. Material Improvement
Alloying: By adjusting the alloy composition of NdFeB magnets, adding some elements that can improve corrosion resistance (such as dysprosium, cobalt, etc.), starting from the material itself, the corrosion resistance of the magnet is improved.
Amorphous alloy: Research and develop amorphous NdFeB magnets. This type of material usually has higher corrosion resistance and better magnetic properties, which is one of the future development directions.
HC Magnets
The company has eight advanced production lines of electroplating process, which can fully ensure customers' various difficult requirements for product coating. And relying on Ningbo's strong front processing capacity, it can stably process and produce N52,N42,N50M,N48H, and other high-performance ndFeb. We are well-known in China and have received welcome from various buyers for on-site inspections, Accept testing and provide free samples Founded in 2017, formerly known as Hangzhou Jiahe Magnetic Ware Factory was established in 2005, Hangzhou Heci Technology Co., Ltd. has been engaged in magnetic industry for 18 years. It is a new high-tech enterprise integrating production, processing, and sales, specializing in the production of permanent magnet materials such as NdFeB magnets. The company is now located in Ningbo, the eastern port city of Yangtze River Delta. The company has the capacity of processing 1000 tons of high performance NdFeB magnets per year. Our products are mainly sold to India, Vietnam and Germany.
Resources
News
- How Do NdFeB Magnets Compare to Other Permanent Magnets in Industrial Applications?
- What are the advantages of using NdFeB Magnets in medical devices?
- Size and shape selection of NdFeB magnets: a key game in engineering applications
- What is the important role of NdFeB Magnets in automobile manufacturing?
- How to determine the magnetic field strength requirements of NdFeB Magnets in specific applications?
- Why NdFeB Magnets are the preferred magnetic material in modern motors and generators?
- How do NdFeB Magnets improve the power output of power tools?
- How do NdFeB Magnets help improve the efficiency of wind turbines?
- How to use NdFeB Magnets to improve the battery performance of electric vehicles?
- How to reduce the demagnetization of NdFeB Magnets?
- When using NdFeB Magnets, how to prevent them from interfering with other devices?
- How to Choose NdFeB Magnets for High-Density Applications?
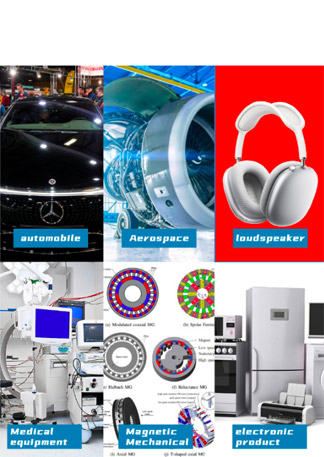