NdFeB magnets have excellent magnetic properties, but they are susceptible to corrosion in some environments. Appropriate surface treatment can effectively enhance their corrosion resistance.
A common method is electroplating. For example, nickel plating forms a dense nickel layer on the surface of NdFeB magnets through electroplating. Nickel has good corrosion resistance and can isolate the magnet from contact with external corrosive media. In order to further improve the corrosion resistance, multi-layer nickel plating can be used to plate three layers of nickel layers with different texture orientations and cross-stacked. According to the crystal texture growth advantage and dendrite growth control mechanism, cross-densification between layers is achieved, and the interlayer bonding force is enhanced, so as to better resist corrosion.
Chemical plating is also an effective surface treatment method. For example, chemical plating of nickel-phosphorus alloy, this coating has the advantages of good uniformity, high hardness, and strong corrosion resistance. In the process of chemical plating, a layer of nickel-phosphorus alloy is deposited on the surface of the magnet through chemical reaction, which can effectively improve the corrosion resistance of the magnet. Moreover, chemical plating can form a uniform coating on the surface of complex-shaped magnets, and is not limited by shape and size like electroplating.
In addition, passivation treatment can also be used. By immersing the NdFeB magnet in a specific passivation solution, a passivation film is formed on its surface. This passivation film can reduce the activity of the magnet surface, improve its stability in the air, and reduce the reaction with corrosive media such as oxygen and moisture, thereby enhancing corrosion resistance.
Coating protection is also a good choice. For example, organic coatings such as epoxy resin coatings and polyurethane coatings are used. These organic coatings have good water resistance, chemical corrosion resistance and insulation properties. Applying it on the surface of the magnet can form a physical barrier to prevent corrosive media from contacting the magnet. At the same time, organic coatings can also choose different colors and glosses according to needs to meet different usage needs and aesthetic requirements.
HC Magnets
The company has eight advanced production lines of electroplating process, which can fully ensure customers' various difficult requirements for product coating. And relying on Ningbo's strong front processing capacity, it can stably process and produce N52,N42,N50M,N48H, and other high-performance ndFeb. We are well-known in China and have received welcome from various buyers for on-site inspections, Accept testing and provide free samples Founded in 2017, formerly known as Hangzhou Jiahe Magnetic Ware Factory was established in 2005, Hangzhou Heci Technology Co., Ltd. has been engaged in magnetic industry for 18 years. It is a new high-tech enterprise integrating production, processing, and sales, specializing in the production of permanent magnet materials such as NdFeB magnets. The company is now located in Ningbo, the eastern port city of Yangtze River Delta. The company has the capacity of processing 1000 tons of high performance NdFeB magnets per year. Our products are mainly sold to India, Vietnam and Germany.
Resources
News
- How Do NdFeB Magnets Compare to Other Permanent Magnets in Industrial Applications?
- What are the advantages of using NdFeB Magnets in medical devices?
- Size and shape selection of NdFeB magnets: a key game in engineering applications
- What is the important role of NdFeB Magnets in automobile manufacturing?
- How to determine the magnetic field strength requirements of NdFeB Magnets in specific applications?
- Why NdFeB Magnets are the preferred magnetic material in modern motors and generators?
- How do NdFeB Magnets improve the power output of power tools?
- How do NdFeB Magnets help improve the efficiency of wind turbines?
- How to use NdFeB Magnets to improve the battery performance of electric vehicles?
- How to reduce the demagnetization of NdFeB Magnets?
- When using NdFeB Magnets, how to prevent them from interfering with other devices?
- How to Choose NdFeB Magnets for High-Density Applications?
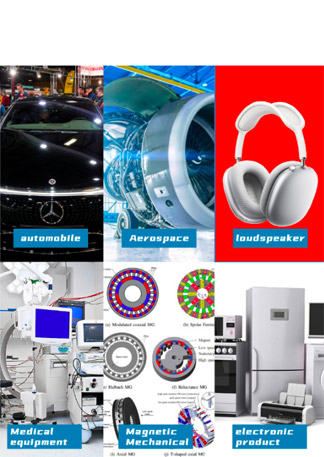