As the permanent magnet material with the highest commercial magnetic energy product, NdFeB magnets are widely used in new energy vehicles, wind power generation, consumer electronics and medical equipment. However, their performance is easily affected by environmental, mechanical and chemical factors. How to maintain the stability of their magnetic properties in daily use?
1. Strict temperature control: avoid irreversible demagnetization
The Curie temperature of NdFeB magnets is usually 310-400°C, but the actual operating temperature needs to be much lower than this threshold. When the temperature exceeds 80°C, some magnets may experience reversible magnetic loss; if exposed to high temperatures above 150°C for a long time, irreversible demagnetization may occur.
Recommended measures:
When used in high temperature environments (such as inside motors), magnets with high temperature resistance grades (such as N42SH, N35UH) are preferred.
Avoid direct contact with heat sources, and add heat dissipation structures or use thermal insulation coatings when necessary.
2. Anti-corrosion treatment: blocking the oxidation reaction path
NdFeB magnets contain active metals such as iron and neodymium. When exposed to a humid or corrosive environment, they are prone to oxidation, resulting in surface powdering and decreased magnetic flux. Studies have shown that unprotected magnets can lose 5%-8% of their magnetic flux within 3 months in an environment with humidity >80%.
Recommended measures:
Use electroplating (nickel, zinc, epoxy resin) or physical vapor deposition (PVD) technology to form a dense protective layer.
Use moisture-proof sealed bags and place desiccant during storage; check the integrity of the coating regularly.
3. Avoid mechanical shock: reduce the risk of structural failure
NdFeB is a brittle material with a tensile strength of only 80-120MPa. Collisions or improper installation may cause microcracks and even cause the magnet to break.
Recommended measures:
Use non-metallic tools (such as plastic tweezers) to operate, and do not knock or drop directly.
Use magnetic fixtures to assist positioning during assembly to reduce the risk of stress concentration.
4. Demagnetization protection: stay away from reverse magnetic field interference
When the external reverse magnetic field strength is close to the coercive force (Hcj) of the magnet, demagnetization may occur. For example, strong electromagnets, MRI equipment or unshielded transformers may generate interference fields.
Recommended measures:
Use a closed yoke structure when designing the magnetic circuit to reduce magnetic leakage.
Use high magnetic permeability materials (such as pure iron) for shielding during storage, and stack adjacent magnets with the same polarity.
5. Regular inspection and data traceability
Regularly monitor the flux attenuation rate through professional equipment (such as gauss meters and flux testers). If the annual attenuation rate exceeds 0.5%, it is necessary to check the environment or operation problems. It is recommended to establish a magnet usage file to record temperature, humidity and performance parameters to achieve life prediction.
HC Magnets
The company has eight advanced production lines of electroplating process, which can fully ensure customers' various difficult requirements for product coating. And relying on Ningbo's strong front processing capacity, it can stably process and produce N52,N42,N50M,N48H, and other high-performance ndFeb. We are well-known in China and have received welcome from various buyers for on-site inspections, Accept testing and provide free samples Founded in 2017, formerly known as Hangzhou Jiahe Magnetic Ware Factory was established in 2005, Hangzhou Heci Technology Co., Ltd. has been engaged in magnetic industry for 18 years. It is a new high-tech enterprise integrating production, processing, and sales, specializing in the production of permanent magnet materials such as NdFeB magnets. The company is now located in Ningbo, the eastern port city of Yangtze River Delta. The company has the capacity of processing 1000 tons of high performance NdFeB magnets per year. Our products are mainly sold to India, Vietnam and Germany.
Resources
News
- How to ensure the performance stability of NdFeB magnets in daily use?
- What Are the Key Factors to Consider When Choosing NdFeB Magnets for Motors?
- How Do NdFeB Magnets Compare to Other Permanent Magnets in Industrial Applications?
- What are the advantages of using NdFeB Magnets in medical devices?
- Size and shape selection of NdFeB magnets: a key game in engineering applications
- What is the important role of NdFeB Magnets in automobile manufacturing?
- How to determine the magnetic field strength requirements of NdFeB Magnets in specific applications?
- Why NdFeB Magnets are the preferred magnetic material in modern motors and generators?
- How do NdFeB Magnets improve the power output of power tools?
- How do NdFeB Magnets help improve the efficiency of wind turbines?
- How to use NdFeB Magnets to improve the battery performance of electric vehicles?
- How to reduce the demagnetization of NdFeB Magnets?
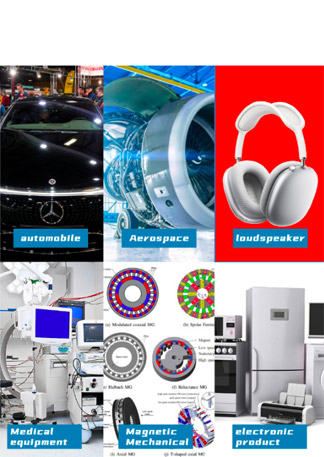