NdFeB magnets have become an indispensable key material in modern motor design due to their high magnetic energy product and excellent magnetic properties. However, when choosing NdFeB magnets, multiple key factors need to be considered to ensure their performance and reliability in specific applications.
The performance of NdFeB magnets mainly depends on their chemical composition and microstructure. High remanence (Br) and high coercivity (Hcj) are its core characteristics, which can ensure the stability and durability of the magnets in complex working environments. When choosing, different grades of NdFeB magnets (such as N35, N42, etc.) need to be selected according to the specific needs of the motor to balance the magnetic properties and costs.
Temperature is an important factor affecting the performance of NdFeB magnets. As the temperature increases, the magnetic properties of the magnets will gradually decrease, and may even cause irreversible demagnetization. Therefore, motors working in high temperature environments need to select NdFeB magnets with high temperature stability (such as high temperature grades with added dysprosium). In addition, heat dissipation design should be considered to reduce the impact of operating temperature on magnet performance.
The cost of NdFeB magnets is usually related to their magnetic properties and production process. Although high-performance magnets are more expensive, their advantages in improving motor efficiency and reducing energy consumption can often bring long-term economic benefits. Therefore, when choosing, it is necessary to weigh performance requirements with budget constraints to avoid excessive pursuit of high performance and unnecessary cost waste.
The manufacturing process of NdFeB magnets has an important impact on their performance and reliability. Injection molding and sintering processes are two common production methods. The former is suitable for magnets with complex shapes, while the latter can provide higher magnetic properties. In addition, strict quality control processes (such as magnetic property testing, appearance inspection, etc.) can ensure the consistency and reliability of magnets, thereby improving the overall performance of the motor.
In practical applications, NdFeB magnets have been widely used in servo motors, permanent magnet synchronous motors (PMSMs), and electric vehicle drive motors. For example, in electric vehicles, high-performance NdFeB magnets can significantly improve the efficiency and power density of motors, thereby extending the vehicle's range.
When selecting NdFeB magnets, it is necessary to comprehensively consider multiple factors such as material properties, temperature stability, cost-effectiveness, manufacturing process, and actual application requirements. Through scientific selection and optimization, NdFeB magnets can achieve optimal performance in motor design and provide strong support for the development of modern electrification and automation technologies.
HC Magnets
The company has eight advanced production lines of electroplating process, which can fully ensure customers' various difficult requirements for product coating. And relying on Ningbo's strong front processing capacity, it can stably process and produce N52,N42,N50M,N48H, and other high-performance ndFeb. We are well-known in China and have received welcome from various buyers for on-site inspections, Accept testing and provide free samples Founded in 2017, formerly known as Hangzhou Jiahe Magnetic Ware Factory was established in 2005, Hangzhou Heci Technology Co., Ltd. has been engaged in magnetic industry for 18 years. It is a new high-tech enterprise integrating production, processing, and sales, specializing in the production of permanent magnet materials such as NdFeB magnets. The company is now located in Ningbo, the eastern port city of Yangtze River Delta. The company has the capacity of processing 1000 tons of high performance NdFeB magnets per year. Our products are mainly sold to India, Vietnam and Germany.
Resources
News
- How to ensure the performance stability of NdFeB magnets in daily use?
- What Are the Key Factors to Consider When Choosing NdFeB Magnets for Motors?
- How Do NdFeB Magnets Compare to Other Permanent Magnets in Industrial Applications?
- What are the advantages of using NdFeB Magnets in medical devices?
- Size and shape selection of NdFeB magnets: a key game in engineering applications
- What is the important role of NdFeB Magnets in automobile manufacturing?
- How to determine the magnetic field strength requirements of NdFeB Magnets in specific applications?
- Why NdFeB Magnets are the preferred magnetic material in modern motors and generators?
- How do NdFeB Magnets improve the power output of power tools?
- How do NdFeB Magnets help improve the efficiency of wind turbines?
- How to use NdFeB Magnets to improve the battery performance of electric vehicles?
- How to reduce the demagnetization of NdFeB Magnets?
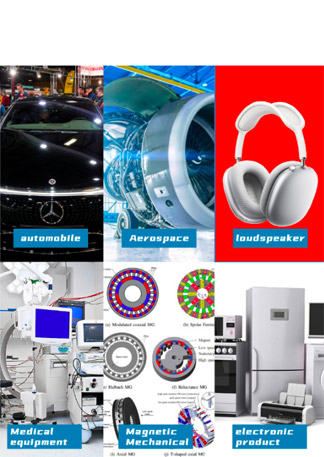